Investing in professional stretch wrap machine repair can lead to better wrapping performance.
Investing in professional stretch wrap machine repair can lead to better wrapping performance.
Blog Article
A Comprehensive Method to Dealing With Stretch Wrap Maker Repair Obstacles
You recognize that stretch cover machines are important for preserving performance in packaging procedures. Issues can arise that interfere with performance. What are the best approaches to ensure your devices run smoothly?
Comprehending Usual Stretch Cover Device Issues
When you depend on stretch cover makers for reliable product packaging, it's important to acknowledge typical problems that can interfere with procedures - stretch wrap machine repair. One widespread issue is inconsistent tension, which can bring about inadequate covering and compromised tons stability. If you observe the film isn't adhering properly, look for worn-out rollers or incorrect settings
One more concern you might encounter is film breakage, frequently triggered by wrong movie kind or equipment malfunctions. Consistently check the device for indications of wear and tear to avoid this.
In addition, maintain an eye on movie accumulation or jams, which can stop production. Commonly, this occurs because of misalignment or debris in the device.
Lastly, inappropriate securing can cause loads coming apart throughout transit. Make sure your device is adjusted correctly to maintain the honesty of your bundles. By remaining watchful and dealing with these problems quickly, you can facilitate smoother operations.
The Relevance of Normal Precautionary Upkeep
Regular precautionary maintenance is important for keeping your stretch cover device running efficiently and efficiently. By consistently examining and servicing your devices, you can spot prospective problems prior to they rise into pricey repair services. This positive approach not just expands the lifespan of your machine however additionally ensures that it operates at peak performance.
You should schedule regular inspections to clean, lubricate, and replace worn parts. Maintaining your device calibrated assists maintain ideal wrapping top quality, reduces waste, and boosts efficiency. Additionally, documenting upkeep tasks develops a trusted history that can educate future decisions.
Do not ignore the importance of training your personnel on upkeep best methods. When every person understands exactly how to care for the device, you decrease the risk of operator error causing break downs. In other words, devoting to regular precautionary upkeep is a wise financial investment that repays in reduced downtime and enhanced efficiency in your operations.
Troubleshooting Strategies for Quick Repair Works
Reliable troubleshooting methods can substantially lower downtime when your stretch wrap equipment experiences problems. Beginning by recognizing the signs. Is the machine not wrapping effectively or is it making uncommon sounds? As soon as you've identified the trouble, refer to the driver's guidebook for support on common concerns and remedies.
Next, inspect the device's setups and controls; occasionally, a basic change can resolve the problem. Evaluate the movie stress and positioning, as incorrect arrangement can lead to wrapping failings. Do not forget electric links; loosened or broken cords can interfere with capability.
If you're still dealing with obstacles, think about running diagnostic examinations if your device has that capacity. Don't hesitate to consult with a technician if you can not deal with the concern rapidly.
Educating Operators for Effective Device Usage
To ensure your stretch cover machine runs at peak performance, proper training for operators is necessary. When operators understand the maker's capabilities, they can maximize its prospective and lessen downtime.
Urge them to practice under supervision, attending to any kind of concerns or problems they might have. Frequently set up correspondence course can keep their skills sharp and aid them adjust to any updates or changes in technology.
Additionally, infuse a culture of liability by equipping operators to report problems or suggest improvements. This proactive strategy not just improves their self-confidence yet likewise adds to the total effectiveness of your procedures. With trained drivers, you'll see less mistakes and raised performance, guaranteeing your stretch cover equipment continues to be a beneficial property.
Constructing a Strong Communication Network In Between Teams
Trained drivers can only carry out at their finest when there's a solid communication channel in between groups. Efficient interaction gets rid of misunderstandings and guarantees everyone's on the same web page pertaining to maker procedures and repair service requirements. Encourage regular check-ins and conferences to go over problems, share insights, and address concerns.
Making use of modern technology, like messaging applications or collective platforms, can boost real-time interaction, making it simpler to report problems and share updates promptly. Assigning clear roles and responsibilities cultivates responsibility, enabling employee to reach out to the right individual when problems arise.
In addition, developing an open atmosphere where everyone really feels comfortable sharing responses can cause innovative remedies. By prioritizing communication, you're not simply improving equipment performance; you're additionally developing a cohesive group that interacts perfectly. This joint spirit eventually leads to quicker repair services and decreased downtime, profiting the entire procedure.
Purchasing Top Quality Replacement Components
When it comes to keeping your stretch wrap makers, buying high quality replacement parts is essential for making sure visit this web-site dependable efficiency and lessening downtime. Affordable alternatives may seem appealing, however they frequently result in more considerable concerns down the line, costing you much more in fixings and lost efficiency. By picking top quality components, you're not simply dealing with a problem; you're improving the total efficiency of your devices.
In addition, top quality parts are usually made to stricter standards, which indicates they'll fit better and function more dependably. This lowers the likelihood of unexpected failures, enabling your operations to run efficiently. Reputable providers typically supply service warranties, offering you tranquility of mind in your financial investment.
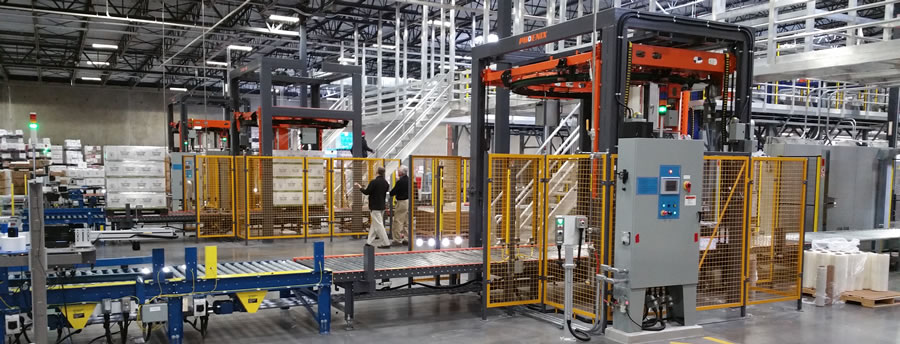
Examining Efficiency Data for Continuous Improvement
To boost your stretch cover maker's performance, you need reliable information collection methods. By assessing performance metrics, you can determine locations for enhancement and boost performance. Recognizing these possibilities not just simplifies operations but additionally minimizes downtime and repair service costs.
Information Collection Methods

Efficiency Metrics Analysis
While reviewing efficiency metrics, it's essential to concentrate on particular data points that directly affect your stretch wrap maker's effectiveness. Begin by tracking cycle times, as they expose exactly how promptly your machine operates under regular problems. Monitor downtime incidents to identify patterns or recurring issues that may require addressing. Watch on film usage, guaranteeing you're not wasting material, which can impact expenses and performance. In addition, analyze result high quality by examining for disparities in the wrapping process. By examining these metrics regularly, you can identify locations requiring focus and take aggressive procedures. This constant examination assists enhance performance, lower expenses, and eventually improve your machine's long life, causing a more efficient covering operation overall.
Determining Renovation Opportunities
As you evaluate efficiency information, you can discover beneficial renovation possibilities that enhance your stretch wrap machine's efficiency. Look for trends in downtime, cycle times, and wrap quality. If frequent break downs correlate with particular operating conditions, you can change processes to reduce these problems.
Often Asked Questions
How Can I Tell if My Machine Needs a Repair or Just Upkeep?
To inform if your equipment requires the original source repair service or simply maintenance, listen for unusual sounds, look for irregular performance, and examine for visible wear. If issues linger after upkeep, it's most likely time for a repair work.
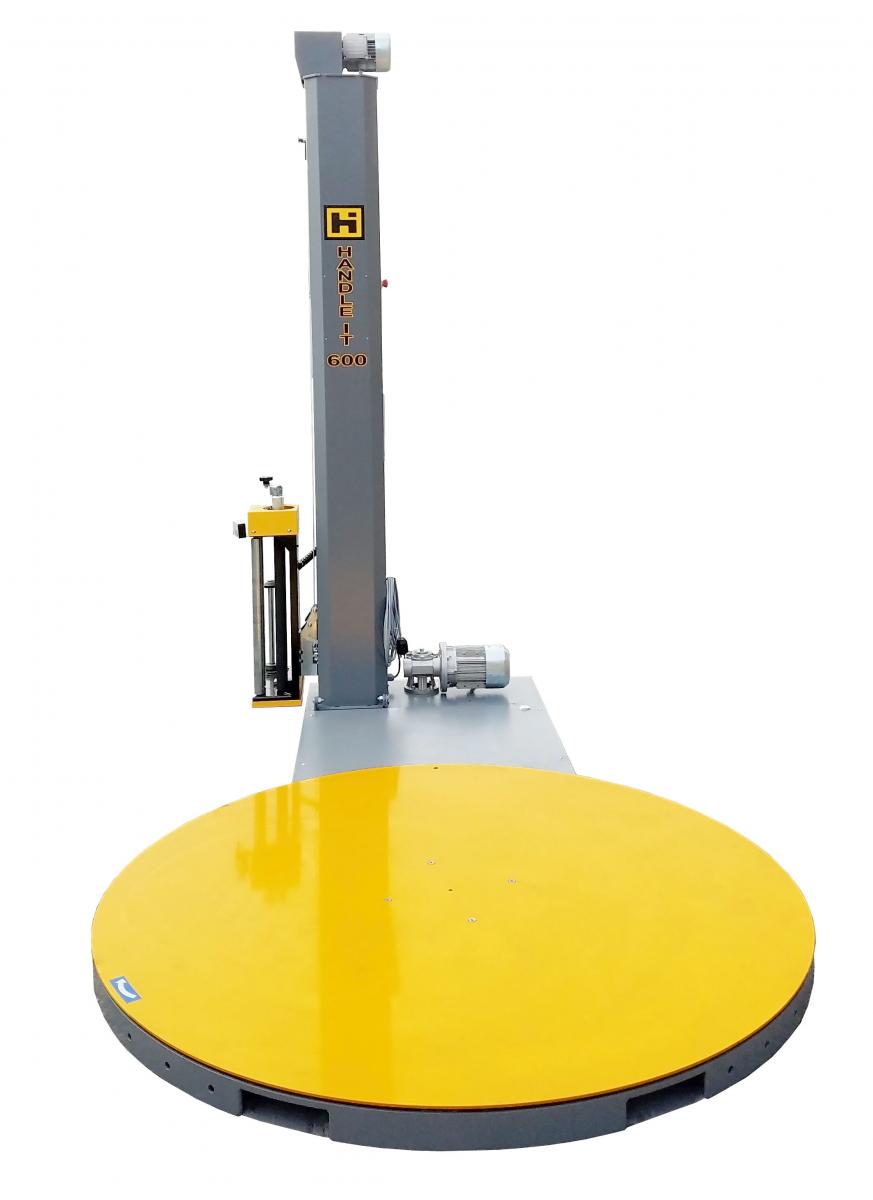
What Is the Ordinary Life-span of a Stretch Wrap Maker?
The average lifespan of a stretch cover maker is usually five to 10 years, relying on usage and maintenance. Routine care can extend its life, so watch on performance and address issues promptly.
Are There Details Brands Understood for Better Reliability?
Yes, some brands are recognized for their dependability. You'll find that firms like Signode and Lantech commonly get positive testimonials - stretch wrap machine repair. Investigating customer comments can help you select a reliable stretch cover maker for your needs
What Are the Indications of Poor Operator Training?
If you observe frequent mistakes, inconsistent covering, or safety cases, those are signs of inadequate operator training. Absence of understanding concerning device features or failure to comply with methods can considerably influence effectiveness and safety and security.
Exactly How Can I Locate a Competent Professional for Repairs?
To discover a certified specialist for fixings, ask for suggestions from sector peers, inspect on-line reviews, and verify qualifications. You might also think about contacting local devices distributors who typically have actually relied on specialists handy.
Verdict
To sum up, dealing with stretch cover equipment repair challenges needs a positive strategy. By prioritizing preventive maintenance, offering complete driver training, and buying quality parts, you can significantly minimize downtime and boost efficiency. Do not neglect the importance of strong communication between teams and continuous assessment of maker result. By implementing these methods, you'll not only improve wrapping quality but also foster a culture of efficiency and improvement in your operations. Stay in advance of concerns prior to they emerge!
Report this page